Power Up Your Safety: The Ultimate Guide to Electrical Tool Inspections
Imagine a construction site humming with activity, workers diligently using power tools to bring a project to life. Now, picture a faulty tool sparking, leading to an accident that could have been prevented. This scenario underscores the critical importance of regular electrical tool inspections. They are not just a formality but a crucial safeguard against potential hazards, protecting both workers and the overall project.
An electrical tool inspection checklist serves as a systematic guide for evaluating the condition of power tools. It's a roadmap to ensuring that every drill, saw, and grinder is in optimal working order, minimizing the risk of electrical shocks, fires, and other workplace incidents. By adhering to a well-defined checklist, organizations can cultivate a culture of safety and prevent costly accidents.
The history of electrical tool inspection checklists is intertwined with the evolution of workplace safety regulations. As the use of electricity in tools became widespread, so did the awareness of potential dangers. Over time, organizations and regulatory bodies recognized the need for standardized procedures to mitigate these risks. This led to the development of formal inspection checklists, which have become an integral part of safety protocols across various industries.
A core issue surrounding electrical tool inspections is the lack of consistent implementation. While many companies recognize the importance of these checks, they may struggle to establish a routine or provide adequate training to personnel. This inconsistency can create vulnerabilities, leaving workers exposed to potential hazards. A robust inspection program requires not just a checklist, but also a commitment to training, monitoring, and continuous improvement.
Electrical tool inspections involve a thorough assessment of various aspects of the tool. This includes checking for damaged cords, loose connections, faulty insulation, and proper grounding. For instance, a visual inspection of a drill cord might reveal cracks or fraying, indicating a potential shock hazard. Similarly, testing the ground fault circuit interrupter (GFCI) on an extension cord ensures that it's functioning correctly, providing an additional layer of protection against electrical shocks.
One key benefit of regular electrical tool inspections is the prevention of workplace accidents. By identifying and addressing potential hazards before they escalate, organizations can significantly reduce the risk of injuries to their workforce. This, in turn, leads to a safer and more productive work environment.
Another advantage is the cost savings associated with preventative maintenance. Identifying and repairing minor issues early on can prevent more extensive and costly repairs down the line. This also extends the lifespan of tools, maximizing the return on investment.
Furthermore, implementing a robust inspection program demonstrates a commitment to workplace safety, fostering a culture of responsibility and care among employees. This can boost morale and improve overall productivity.
An effective inspection program involves several steps. First, establish a clear schedule for inspections, ensuring that all tools are checked regularly. Second, train personnel on how to properly use the checklist and conduct thorough inspections. Third, maintain detailed records of all inspections, documenting any identified issues and corrective actions taken. Finally, regularly review and update the checklist to reflect changing regulations and best practices.
Advantages and Disadvantages of Electrical Tool Inspection Checklists
Advantages | Disadvantages |
---|---|
Improved Safety | Time Consuming |
Cost Savings | Requires Training |
Increased Productivity | Potential for Oversights |
Best Practices:
1. Use a standardized checklist: This ensures consistency and thoroughness.
2. Train personnel: Equip employees with the knowledge and skills to conduct effective inspections.
3. Document findings: Maintain detailed records of all inspections and repairs.
4. Regularly review and update the checklist: Keep the checklist current with industry standards and regulations.
5. Establish a clear inspection schedule: Ensure that inspections are conducted consistently and frequently.
FAQs:
1. How often should tools be inspected? - Depends on frequency of use, but generally before each use or at least weekly.
2. Who should conduct inspections? - Trained personnel familiar with the tools and the checklist.
3. What should be included in the checklist? - Cords, plugs, insulation, grounding, and overall functionality.
4. What happens if a tool fails inspection? - Remove from service immediately and repair or replace.
5. Where can I find a sample checklist? - Safety organizations and online resources offer various templates.
6. What are the consequences of not inspecting tools? - Increased risk of accidents, injuries, and costly repairs.
7. How can I improve my inspection process? - Regular training, feedback, and updates to the checklist.
8. Are there any legal requirements for tool inspections? - Yes, OSHA and other regulatory bodies have specific requirements.
Tips and tricks: Use brightly colored tags to indicate inspection status, create digital checklists for easy access and record-keeping, and conduct regular refresher training for inspection personnel.
In conclusion, implementing an electrical tool inspection checklist is not merely a best practice, but a fundamental requirement for maintaining a safe and productive work environment. By diligently adhering to a comprehensive checklist, organizations can effectively mitigate the risks associated with electrical hazards, safeguarding their workforce and preventing costly accidents. The benefits extend beyond immediate safety, encompassing long-term cost savings, increased productivity, and a strengthened culture of responsibility. Committing to regular inspections and continuous improvement is an investment in the well-being of employees and the overall success of any organization. Take action today to establish a robust inspection program and power up your safety protocols. Remember, a proactive approach to safety is always the best approach.
Navigating loss your guide to ziemer funeral home central chapel
Unlocking the power of male emojis a deep dive
Decoding the hollow heart what does mean on instagram












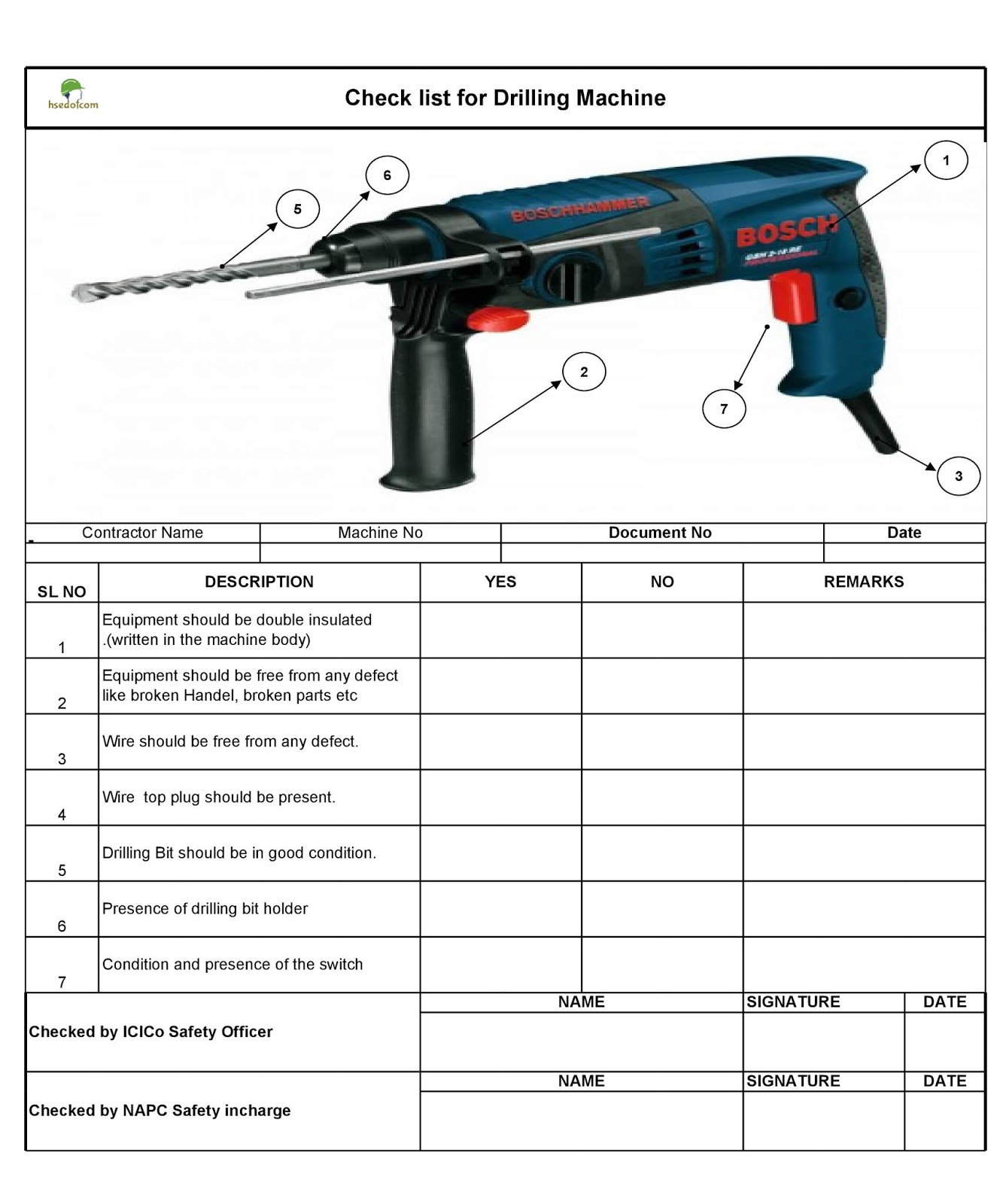